Work Page 7-20
1920's Ludwig "The Ace"
19 fret tenor
Walnut construction
Carved heel
"Standard Art" resonator
Celluloid peg head overlay
Walnut construction
Carved heel
"Standard Art" resonator
Celluloid peg head overlay
INITIAL PICS
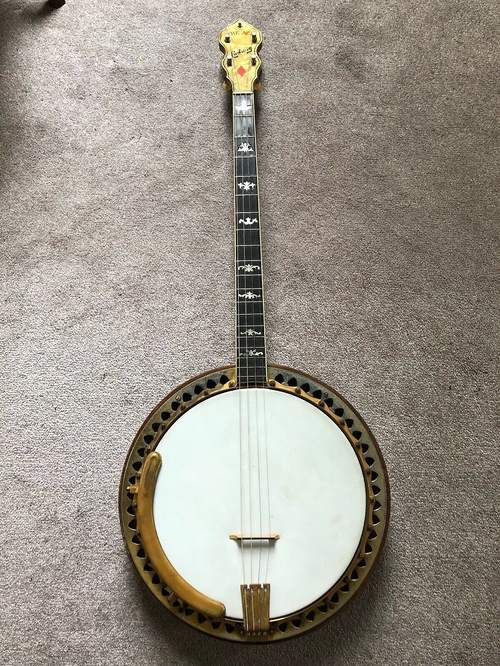
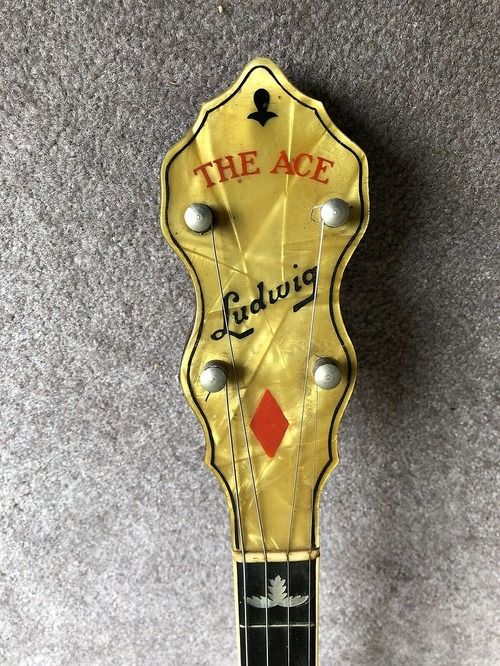
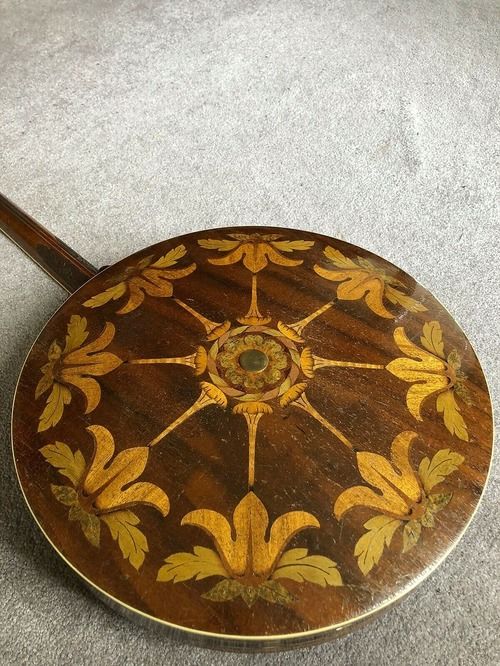
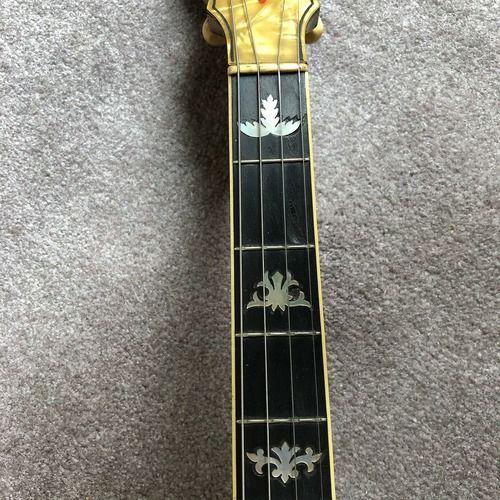
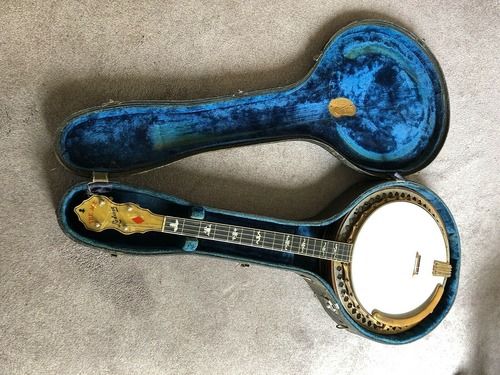
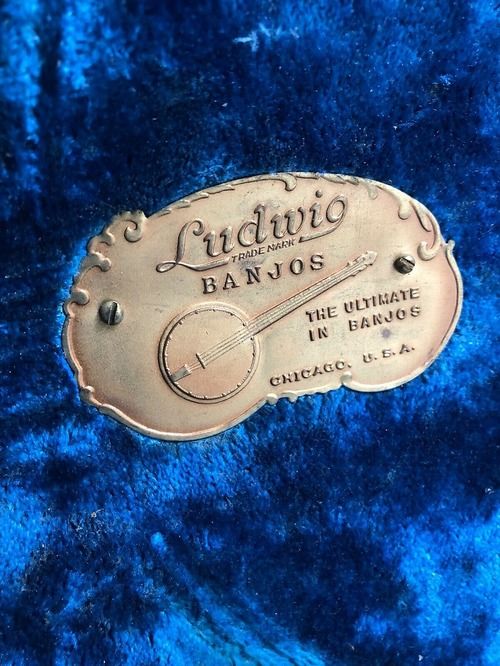
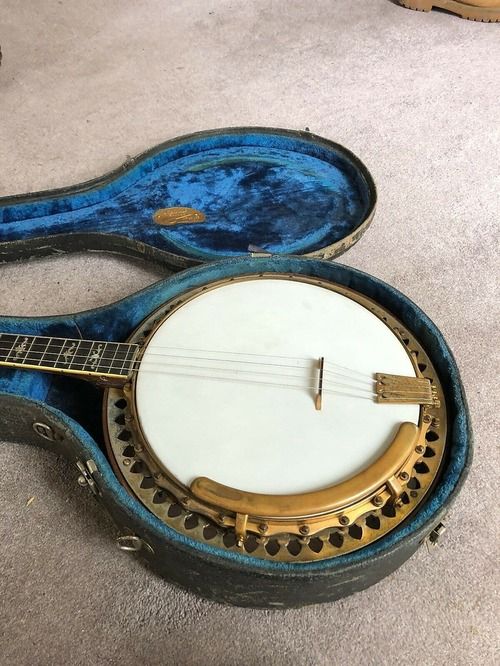
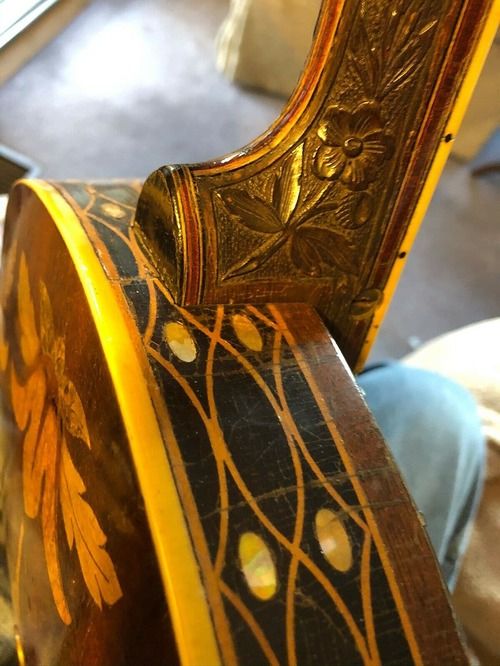
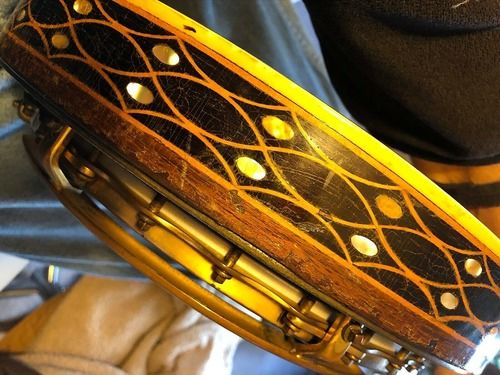
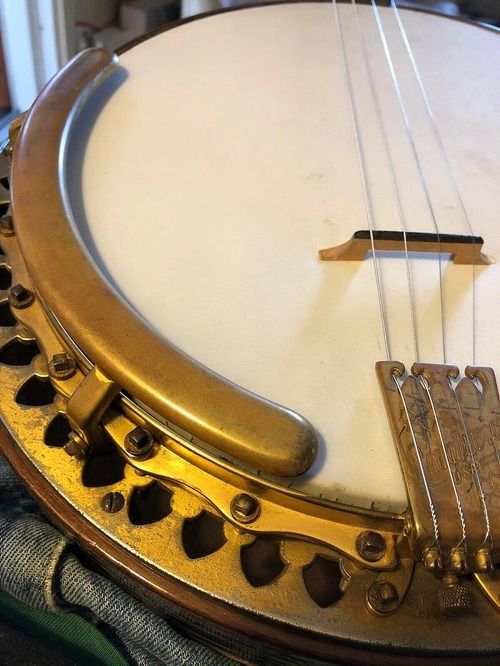
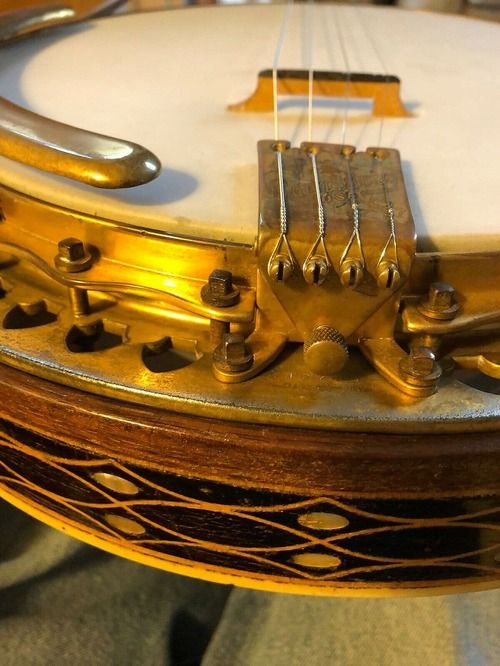
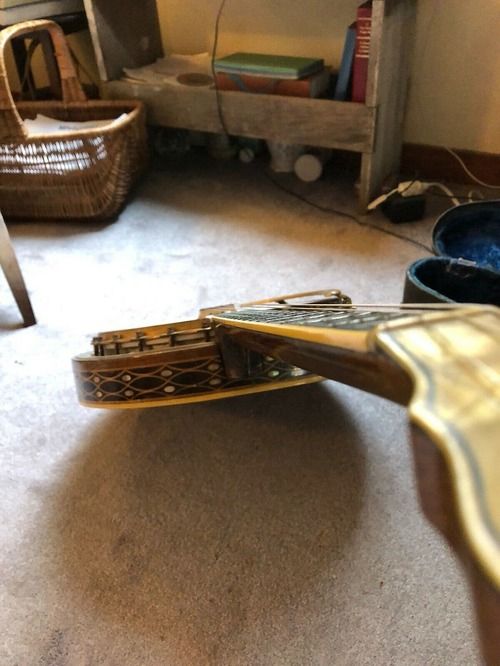
23" scale
Patented cammed neck angle adjuster
Tone enhancing cone (accessory) , in the resonator
Cast metal flange-Brass tension hoop
Repairs
This banjo came to me in generally fair condition.
Worn plating, worn finish, some minor wear on fingerboard.
It has all of its original parts, with the exception of tuners.
It's major issue, will be its flange.
The arrowhead flange on this model, is casted pot metal.
Over time, many banjos that used cast metal flanges, over time, have major issues. Cast metal does not have the strength as a pure metal such as brass, so under tension, they tend to pull upwards over the course of many years.
Some go completely awry, and disentergrate, and others break out in pieces, while some just warp.
And some...never have an issue at all.
I attribute all of these things to "What went into the pot", when making the castings.
Ludwig used Doehler Die Casting Co.
At its peak during the mid-20th century, the Doehler-Jarvis Company (1908-1998) was the largest producer of die-cast metal in the world.
By the part # on the flange, you can see the Doehler die stamp.
This can also be seen on all Pre-war Gibson one piece flanges.
(Which also suffer from the same maladies)
As I disassemble it to form a plan of attack, you can see that the Ace flange has casted into it, the square holes, that are for alignment of the dowel stick through the rim.
This is as far as I know, unique to the ACE, but other models I have not seen or worked upon, may implement it.
Te Resonator is an upgrade from the factory, to the "Standard Art" model which was a high end Ludwig.
It has a neck notch cut into it to accept the ACE flange design.
Other top tension Ludwigs
Worn plating, worn finish, some minor wear on fingerboard.
It has all of its original parts, with the exception of tuners.
It's major issue, will be its flange.
The arrowhead flange on this model, is casted pot metal.
Over time, many banjos that used cast metal flanges, over time, have major issues. Cast metal does not have the strength as a pure metal such as brass, so under tension, they tend to pull upwards over the course of many years.
Some go completely awry, and disentergrate, and others break out in pieces, while some just warp.
And some...never have an issue at all.
I attribute all of these things to "What went into the pot", when making the castings.
Ludwig used Doehler Die Casting Co.
At its peak during the mid-20th century, the Doehler-Jarvis Company (1908-1998) was the largest producer of die-cast metal in the world.
By the part # on the flange, you can see the Doehler die stamp.
This can also be seen on all Pre-war Gibson one piece flanges.
(Which also suffer from the same maladies)
As I disassemble it to form a plan of attack, you can see that the Ace flange has casted into it, the square holes, that are for alignment of the dowel stick through the rim.
This is as far as I know, unique to the ACE, but other models I have not seen or worked upon, may implement it.
Te Resonator is an upgrade from the factory, to the "Standard Art" model which was a high end Ludwig.
It has a neck notch cut into it to accept the ACE flange design.
Other top tension Ludwigs
THE PLAN....
Since there is no repairing cast metal, the ACE flange will be retired
I have sat and studied the other top tension Ludwig design, from pieces and parts in the shop, and have made a command decision.
To be able to use this instrument, it will require an extensive modification of Neck/Resonator, utilizing off the shelf Ludwig parts, from other models.
The goal is a nice playable instrument that in all respects, close as I can come to its original look.
So...
I will take a nickel plated Brass flange from a Rivera plectrum and modify it to fit the heel changes necessary on the Ace neck.
So a notch will be cut from it, as in the ACE flange.
Resonator will get cleaned on the inside and some new finish inside and out.
Flange serial numbers are fairly close.
The positive, is that the brass flanges are stronger, and have a larger more substantial bear edge and will make for a more full tone.
You an see that difference in the pics
The neck, shown by the Rivera neck, shows the type of cut out I must make on the heel. You can see on the ACE neck, where it s not carved, is the basic amount of wood to be removed from each "cheek", and under the fingerboard.
Also, I will have to fill the neck notch to the style of the other top tension models, where they have a square hole for the dowel like is cast on the original flange.
I will take that section from a bastard "Dixie " model resonator, and seal it into the cut out
I removed the cams from the neck to show how they work, on reassembly.
After making the neck cuts (not for the faint of heart), I can see that this just may work as planned, so onward. Made the filler wood for the neck notch and sealed it all in. The bonus of using something original here, is that the radius is exact, as both resonators are identical in diameter.
I did to elevate it, to work on the tenor neck.
Then to correct a factory error, I had to move the hardware attached to the dowel, from bottom to top.
All Ludwig's are this way, the bolt head has to be upwards, to easily get to it.
I'm sure someone in QC at Ludwig let that by, this never had a dowel reset in its life. I know of no one that ever successfully reset a Ludwig dowel.
By design, pretty impossible.
Then I filled the old notch made by the hardware on the dowel and refinished it
Next, to fill in the gap a the front, of the resonator so that the Rivera style dowel centering ferrule can work, will require another block so that it can mount to that. I used another section of the donor Dixie resonator to form it. Also, nice to have the same radius for good fit.
Now I will take that all apart and "Finish the finish"
Celluloid peg head overlay is lifting so glue /clamp...good to go.
Also, some loose center laminates in the neck were filled and sealed
Someone had already sent it for a heat press and new frets, so that work will be tested when I get it together and back to tension
Polished and waxed the overlay.
Now the neck is taking on final finish with the resonator,shown in the last pic of this sequence.
I have sat and studied the other top tension Ludwig design, from pieces and parts in the shop, and have made a command decision.
To be able to use this instrument, it will require an extensive modification of Neck/Resonator, utilizing off the shelf Ludwig parts, from other models.
The goal is a nice playable instrument that in all respects, close as I can come to its original look.
So...
I will take a nickel plated Brass flange from a Rivera plectrum and modify it to fit the heel changes necessary on the Ace neck.
So a notch will be cut from it, as in the ACE flange.
Resonator will get cleaned on the inside and some new finish inside and out.
Flange serial numbers are fairly close.
The positive, is that the brass flanges are stronger, and have a larger more substantial bear edge and will make for a more full tone.
You an see that difference in the pics
The neck, shown by the Rivera neck, shows the type of cut out I must make on the heel. You can see on the ACE neck, where it s not carved, is the basic amount of wood to be removed from each "cheek", and under the fingerboard.
Also, I will have to fill the neck notch to the style of the other top tension models, where they have a square hole for the dowel like is cast on the original flange.
I will take that section from a bastard "Dixie " model resonator, and seal it into the cut out
I removed the cams from the neck to show how they work, on reassembly.
After making the neck cuts (not for the faint of heart), I can see that this just may work as planned, so onward. Made the filler wood for the neck notch and sealed it all in. The bonus of using something original here, is that the radius is exact, as both resonators are identical in diameter.
I did to elevate it, to work on the tenor neck.
Then to correct a factory error, I had to move the hardware attached to the dowel, from bottom to top.
All Ludwig's are this way, the bolt head has to be upwards, to easily get to it.
I'm sure someone in QC at Ludwig let that by, this never had a dowel reset in its life. I know of no one that ever successfully reset a Ludwig dowel.
By design, pretty impossible.
Then I filled the old notch made by the hardware on the dowel and refinished it
Next, to fill in the gap a the front, of the resonator so that the Rivera style dowel centering ferrule can work, will require another block so that it can mount to that. I used another section of the donor Dixie resonator to form it. Also, nice to have the same radius for good fit.
Now I will take that all apart and "Finish the finish"
Celluloid peg head overlay is lifting so glue /clamp...good to go.
Also, some loose center laminates in the neck were filled and sealed
Someone had already sent it for a heat press and new frets, so that work will be tested when I get it together and back to tension
Polished and waxed the overlay.
Now the neck is taking on final finish with the resonator,shown in the last pic of this sequence.
7-18 update- Assembly
I decided to use a vintage 10-3/4 Remo top frosted,that was the correct crown height.
I used Nikolas Lacquer, gold fill, to do the oxidized brass armrest and tailpiece, and the resonator plug.
It is a tried and true brass instrument lacquer finish, since the 1800s
Also I will use nickel plated tension bolts to further mix/match the plating. The gold is worn from the tops of the orig and I want "shinier" Anyone that remembers Vega's "Soloist" model, it was a mixed plating instrument.
Also, I will use the correct tuner for the instrument, which is the "Planet" style that came on it.These too, will be nickel and ivoroid buttons
The "Tone cone" for the resonator, mocked up on a faux cymbal stand should show us all, where Ludwig came up with the idea, :):)
I will have my son in law Kenny Sharretts, "Pro Drum Tech" weigh in on that.
Also, I show the 3 tools it takes to work on a Ludwig banjo.
They are built to very close tolerances for the day, and this is why you can mix/match some of the parts and pieces over the years that they made banjos.
They made very few designs, with only embellishments /exotic woods/ gold plating's to have higher end models available to compete with other makers.
The Neck Cams
I show basically how they fit into the neck, and how when you screw in the side screws, it pulls the wedges, which actuate the posts, that contact the rim assembly and give the ability to push the neck angle back.
Simple, elegant, functional.
Its best to see it apart once, to "Get it"
So then, I cinched all the new hardware up, added the tuners.
Strung it to pitch, GDAE 40-30-20W-14S
It is gutsy sounding, piercing, could hold its own with any archtop banjo in an Irish session, if the player has talent.
Quick note decay up on the bridge.
Now it is an all brass rim assembly, you cannot look for warmth in it, without subtle pick attacks.
But up by the neck, it can get warm tones.
Great for single string, or punching a hard rhythm as a CGDA tuned instrument.
I feel that it was worth the effort, and it will not be something that will break the pocketbook, it is just a payers instrument, not some "collectible", with a fresh outlook on life, and it needs a good home.
I will place the final pics on My Tenors for sale page, but here is one.
Thanks for looking, sharing, Inquiring
Vinnie
I used Nikolas Lacquer, gold fill, to do the oxidized brass armrest and tailpiece, and the resonator plug.
It is a tried and true brass instrument lacquer finish, since the 1800s
Also I will use nickel plated tension bolts to further mix/match the plating. The gold is worn from the tops of the orig and I want "shinier" Anyone that remembers Vega's "Soloist" model, it was a mixed plating instrument.
Also, I will use the correct tuner for the instrument, which is the "Planet" style that came on it.These too, will be nickel and ivoroid buttons
The "Tone cone" for the resonator, mocked up on a faux cymbal stand should show us all, where Ludwig came up with the idea, :):)
I will have my son in law Kenny Sharretts, "Pro Drum Tech" weigh in on that.
Also, I show the 3 tools it takes to work on a Ludwig banjo.
They are built to very close tolerances for the day, and this is why you can mix/match some of the parts and pieces over the years that they made banjos.
They made very few designs, with only embellishments /exotic woods/ gold plating's to have higher end models available to compete with other makers.
The Neck Cams
I show basically how they fit into the neck, and how when you screw in the side screws, it pulls the wedges, which actuate the posts, that contact the rim assembly and give the ability to push the neck angle back.
Simple, elegant, functional.
Its best to see it apart once, to "Get it"
So then, I cinched all the new hardware up, added the tuners.
Strung it to pitch, GDAE 40-30-20W-14S
It is gutsy sounding, piercing, could hold its own with any archtop banjo in an Irish session, if the player has talent.
Quick note decay up on the bridge.
Now it is an all brass rim assembly, you cannot look for warmth in it, without subtle pick attacks.
But up by the neck, it can get warm tones.
Great for single string, or punching a hard rhythm as a CGDA tuned instrument.
I feel that it was worth the effort, and it will not be something that will break the pocketbook, it is just a payers instrument, not some "collectible", with a fresh outlook on life, and it needs a good home.
I will place the final pics on My Tenors for sale page, but here is one.
Thanks for looking, sharing, Inquiring
Vinnie